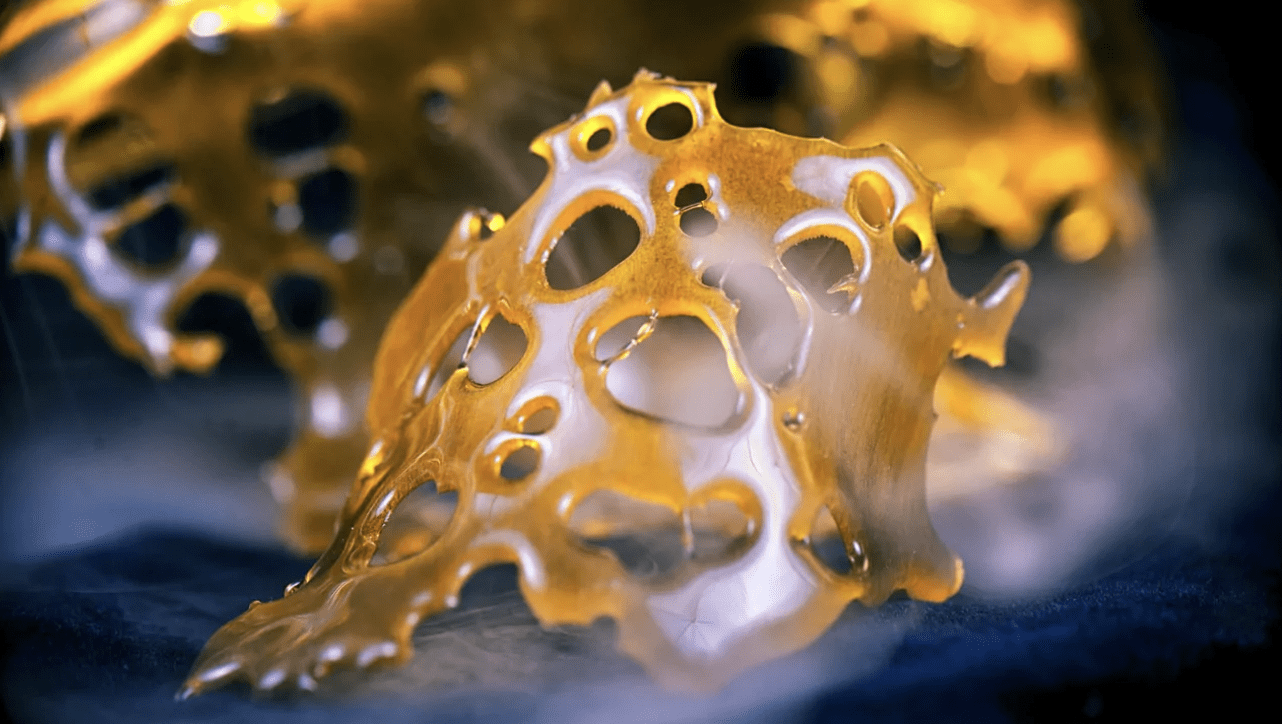
17 Apr Adopting Automated Cannabis and Hemp Extraction Solutions
Originally posted on Analytical Cannabis.
Thanks to the implementation of automatic packaging and labeling machines and automatic sensors in controlled environment agriculture greenhouses, automation has already helped the cannabis sector to reach peak new levels of efficiency.
Until very recently, however, the cannabis extraction process had always been the realm of manual labor. But with the explosive growth of the cannabis and CBD markets and the accelerating demand for high-quality products, automated cannabis and hemp extraction solutions are quickly becoming the standard within the extraction sector.
The adoption of automation for cannabis and hemp extraction
The industry’s shift toward automation began slowly. A far cry from waking up and discovering your job had been replaced by some robot, the first automated systems to be used in cannabis and hemp extraction were usually implemented as a way for extraction operations to better serve their staff members.
“Going from the extractors where you had almost everything manual, to the extractors where you press a button and walk away, there was this period of time in the middle,” Alisia Ratliff, CEO of Victus Consulting Ventures, told Analytical Cannabis.
“The solvent recovery piece would be something that was automated. And the extraction itself would be something that’s automated to where you are not actually funneling in your liquefied CO2, or you’re not funneling in your butane or ethanol. That would be something that the system is doing for you,” Ratliff continued. “But when it’s separation time, you might be the one that’s controlling the pressure vessel.”
As time has passed, automation has been applied to even more of the extraction workflow. Systems have been developed that are able to connect necessary hoses or open and shut valves as soon as it is needed, so expert staff are no longer required to do these menial, repetitive tasks, and can instead use their expertise elsewhere in the process.
Automation brings new era of safer production
“Anytime you could kind of move to automation, the benefits you get are enormous. When you move to automation, you get better consistency, you get better efficiencies, better reproducibility, you get less errors that are operator driven,” Deepank Utkhede, chief operating officer of the Colorado-based CBD extract manufacturing firm Vantage Hemp, told Analytical Cannabis.
Vantage Hemp currently operates a fully-automated hydrocarbon extraction system. Automated systems for hydrocarbon extraction were not particularly common when they began operations, Utkhede recalls. However, the volatility of hydrocarbon solvents necessitates extremely stringent safety precautions. The dangers of not implementing such precautions was illustrated by an explosion at one clandestine extraction operation in Los Angeles that Utkhede remembers occurring while his colleagues were searching for apparatuses. Adopting an automated system quickly became Vantage Hemp’s main priority.
“Most of these systems at the time we were looking were manual, you had to remember to close a valve, open a valve, all of these things,” Utkhede said. “When we’re looking for equipment, it really was, ‘how do we make this as safe as possible?’, and the best way is to have an automated system. There are only two manual parts to the process. One is loading and unloading biomass out of the extraction columns, the other one is pressing ‘start.’”
In addition to reducing the direct exposure risk to dangerous solvents, automated equipment also has the benefit of automated fail-safes that can be applied more quickly, and at much lower risk, than if a staff member was required to manually shut down operations.
“You can have valves that when you lose power, they go to an automatic closed state or an automatic open state. You can’t do that with manual valves,” Utkhede said. “If you lose power during a [manual] cycle, you could have a very dangerous situation where you’ve got all these valves that shouldn’t be open, and you’d have to go in and know which ones to close. But in an automated system, because everything’s hooked up to the control panel, when you lose part of that panel it shuts everything off in the right sequence.”
Enhancing compliance with GMP
Making sure that employees at an extraction facility are safe is naturally one of the most important facets of running an extraction facility. But automation can also help ensure the safety of product consumers by enabling easier compliance with Good Manufacturing Practice (GMP) principles for pharmaceutical-quality products.
“GMP is all about consistency. The reason why you have batch records, SOPs and procedures, training, and all that stuff is consistency,” Utkhede said. “When you say you’re going do something and it’s going to produce something, you do it and it produces this.”
Consistency is a natural benefit of automated processes, since many opportunities for human error are eliminated. But automated systems can also help extractors keep up with the required documentation needed for GMP certification, as Ratliff explained.
“You want to make sure that you have these GMP processes in place to where you’re tracking, you have traceability of that batch and what went on with the batch, you’re tracking the equipment maintenance,” she said. “A lot of these automated extractors, they will log that data for you. It just depends on what you purchase and what your add-ons are.”
“If you’re tracking your data appropriately, if you are running a GMP facility that is keeping those good documentation records, then you can learn so much about each batch, and you are able to make those decisions in the future on what you need to do to optimize or improve,” Ratliff said.
Efficiency and staff morale
Another, often under-recognized, perk of using automation in the cannabis and hemp extraction process is the positive impact on employee morale.
“I had a staff member in my career – an amazing, amazing girl – she was on the night shift and I had her doing a lot of labeling and the filling of the capsule bottles,” Ratliff recalled. “As soon as we introduced an automated machine, she was just ecstatic. She was like, ‘Now I can actually do other things, I can use my brain a little bit more, I don’t have to just sit here and do all this tireless stuff!’”
“The people who are actually doing these processes, when you go automated, you are making their job easier,” Ratliff continued. “The morale in your staff is going to go through the roof when you have automated equipment.”
Morale was not the only facet to improve though. Ratliff’s new automated system was incredibly consistent, which meant fewer bottlenecks where products had to be pulled and corrected, and an increased overall efficiency.
This is true for all aspects where automation is applied in cannabis and hemp extraction. As Utkhede put it when talking about automated quality control systems, “a machine is always the same; its ability to identify defects doesn’t change by how much sleep it got, or how much coffee it drank before starting its shift.”
Instead of being put to work to manually carry out repetitive tasks, staff can instead fill supervisory roles where they validate that these automated processes are working as they should and use their expertise to make any tweaks or adjustments that might be required elsewhere.
“When we started processing, back in 2020 when our facility was first up and running, it was similar to what we’re doing now, but it’s not the same as what we’re doing now,” Utkhede said. “We’re seeing efficiency gains, we’re seeing subtle tweaks.”
Keeping up with consumer trends
Compared to other sectors, the cannabis and hemp extraction business is still a young one. But in recent years, consumers have become much more knowledgeable about the type of extracts they are buying and are increasingly more interested in how their extracts are being made.
While CO2 extraction is generally thought to be the most popular choice of extraction method among extraction firms, there are some consumers who want a more “artisanal” approach. For the consumers who follow this growing trend, solventless extraction methods are generally seen as the most desirable extracts because they follow a more “natural” process.
One of the most common methods for solventless extraction is ice water extraction (IWE), where oily cannabinoids are extracted from cannabis and hemp biomass by placing the material in large vats of icy water and agitating the material.
“If you look at a lot of the equipment that’s on the market for solventless [extraction], you now have automated overhead stirrers that come down into the tank,” Ratliff said. “You have automated pumps pumping that trichome-filled water into the filter stack. They are actually shaking it out for you, now that you have mechanical shakers.”
All of this adaptation frees up more time for staff to be utilized downstream, Ratliff says. Instead of being required to physically mix these vats, employees’ time can be spent on more valuable applications such as quality control, or in managing the molding and pressing of the biomass material.
As the scientific practices and legal frameworks relating to the cannabis and hemp extraction sector continue to develop, and automated equipment manufacturers continue to respond in kind, novel innovations are seemingly always just around the corner. And such innovations are ones that the industry is keen to embrace.
“It’s exciting times,” Utkhede said. “I’m excited to see where we end up because it’s definitely not going to be where we are right now. We’ll see where the technology goes, see where the market goes, and hold on for the ride.”
Sorry, the comment form is closed at this time.